https://xtech.nikkei.com/atcl/nxt/column/18/00001/08616/?n_cid=nbpnxt_mled_dmh
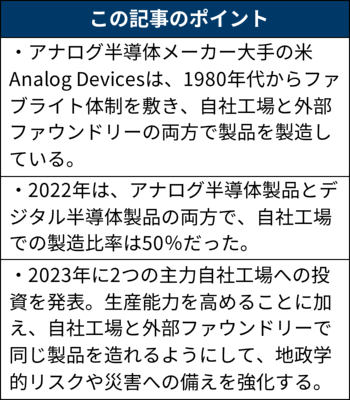
アナログ半導体の製造にはノウハウが必要で、基本的に内製だろう——こう考えている人は少なくないだろう。その考えをいとも簡単に否定したのは、アナログ・デバイセズ代表取締役社長の中村勝史氏(図1)の発言だ。「米Analog Devices(アナログ・デバイセズ、以下ADI)ではアナログもデジタルも内製は半分で、残りは外部のファウンドリーに製造委託している」(同氏)。
ADIは1965年創業の老舗半導体メーカーである。最初の製品はオペアンプモジュールだった。1970年代にはデータコンバーター(A-D変換器/D-A変換器)ICを発売した。1980年代には、A-D変換器の後段に接続するICが重要になるとしてDSP(Digital Signal Processor)へ進出している。2016年に電源ICメーカー大手の米Linear Technology(リニアテクノロジー)を、2020年に中堅アナログ半導体メーカーの米Maxim Integrated Products(マキシム・インテグレーテド・プロダクツ)をそれぞれ買収した。現在、ADIは約7万5000品種を超える製品をそろえている。売上高は、大きい順にデータコンバーター、アンプ、電源IC、有線通信/インターフェース、無線通信、DSPだという。2022会計年度の売上高は120億米ドル(約1兆8100億円)で、従業員数は約2万5000人である。
中村氏によれば、ADIがファブライト化、すなわち、自社の工場と外部のファウンドリーの両方でICを製造するようになったきっかけは、台湾TSMC(台湾積体電路製造)が創業したことだという。TSMCは1987年の創業である。デジタルIC(ロジックIC)の半導体メーカーでファブライト化の動きが目立つようになったのは、2011年にTSMCが28nm世代プロセスでの製造を始めた頃だ。それに比べて、ADIがファブライトになったのは非常に早かった。
ADIの2022年における内製比率(売上高ベースの比率)は、前工程(拡散工程)で50%、後工程のうちテストは80%、後工程の組み立て(パッケージング)は20%である(図2)。中村氏によれば、この内製比率は結果であって、目標は特に設置していない。従って、年によって比率は変動するという。現在、ADIが製造委託しているファウンドリーは10の国や地域にある約20社で、拠点数は合計で約50に上る。この中には日本にあるファウンドリーも含まれるが、「具体的な社名は明かせない」(同氏)という。なお先端ロジックプロセスを手掛けるTSMCや韓国Samsung Electronics(サムスン電子)もアナログICの製造受託を行っている。またアナログ専業のファウンドリーではイスラエルTower Semiconductor(タワーセミコンダクター)が大手として知られている。この他に、特定のプロセスを扱う結構な数のアナログファウンドリーが世界にはある。
自社でも外部ファウンドリーでも造れる体制へ
ADI自身の主力工場は、米オレゴン州のビーバートンと、アイルランドのリムリックの2カ所である。今後の半導体需要の高まりと供給安定化に向けて、2カ所の製造拠点への大型投資を行うことを今年(2023年)発表した。具体的には、ビーバートン工場には10億米ドル(約1510億円)を投じて主に180nmプロセスの製造能力を約2倍に引き上げる 日本語ニュースリリース 。同工場のクリーンルームの総面積は約1万960平方メートルへ拡張される(図3)。
リムリックへは6億3000万ユーロ(約1020億円)を投じる 日本語ニュースリリース 。これによって、約4180平方メートルの新たな研究開発・製造施設を建てる。リムリックの生産能力は3倍以上になる。なおリムリックの主な製造プロセスは350n~700nmである。さらに、電源ICの製造を担う米ワシントン州カマスの工場の生産能力も1.5倍に引き上げる計画だという。
今回の生産能力増強では、これまでにない取り組みがある。すなわち、自社工場と外部ファウンドリーとで同じ製品を造れるようにする。これまでは、製品ごとに製造拠点は決まっていて、自社工場で造る製品は外部ファウンドリーには委託しないし、外部ファウンドリーに製造委託した製品は自社工場では造ることはなかった。いわゆる地政学的リスクや災害発生時のレジリエンスに向けて、自社でも外部ファウンドリーでも造れる体制にする。
0 コメント:
コメントを投稿