https://www.nikkei.com/prime/tech-foresight/article/DGXZQOUC2894K0Y4A220C2000000?n_cid=NPMTF000P_20240229_a15
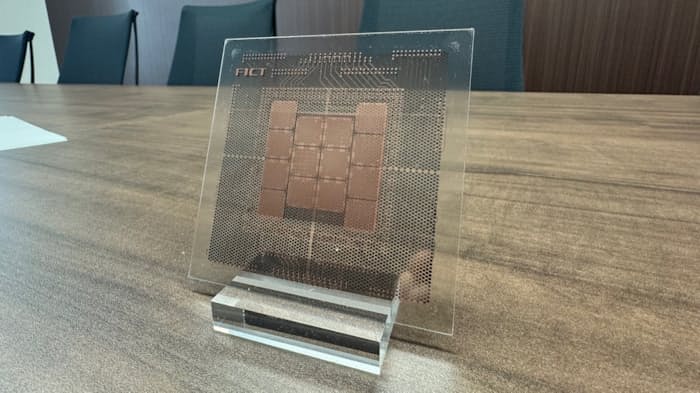
半導体のパッケージ基板材料としてガラスが注目されている。半導体パッケージや基板を手がけるFICT(長野市)は、コア層のガラスを多層化した基板(マルチガラスコア基板)を開発した。実用化に向けてダイシング(切断)時に割れる課題を解決したほか、高温下の反り量や熱膨張率が抑えられることから、チップレット集積でも有利になる。
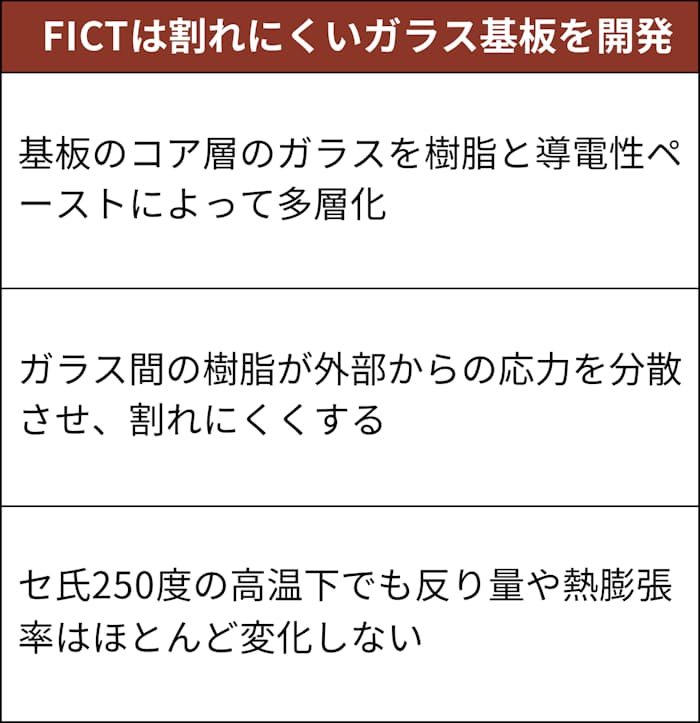
多層化で割れの問題を解決
ガラス基板の実用化に向けた大きな課題の1つは、基板のダイシング時に発生する「セワレ」と呼ばれる現象だ。新開発のマルチガラスコア基板「G-ALCS(Gアルシス)」は、このセワレに対応した。
ガラス基板は、コア層の上下に、配線層と絶縁層を重ねたビルドアップ層を何層も重ねた構造となっている。このビルドアップ層の層数を増やすと、ダイシング時にビルドアップ層の応力によってガラスが裂けるように割れてしまう。「我々のシミュレーションでは、単層のガラスをコア層として使った場合、ビルドアップ層の層数は4層ぐらいが限界だと分かっている」とFICTテクノロジ本部先行技術開発部部長の飯田憲司氏は言う。
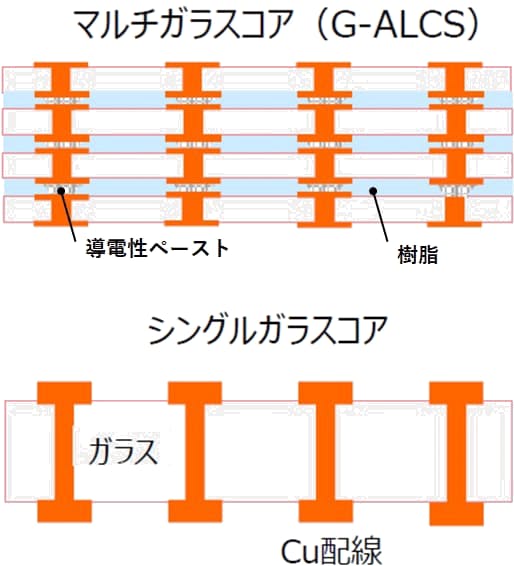
そこでFICTは、樹脂と導電性ペーストを使ってコア層のガラスを多層化した。コア層のガラス間にある樹脂が外部からの応力を分散させる。単層品で応力が集中していた箇所について、多層品では応力を5分の1に抑えられるという。
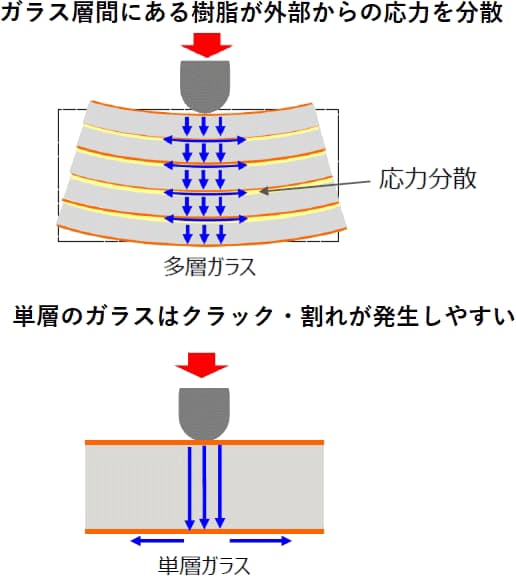
高温下の反り量や熱膨張率がほとんど変化しないという利点もある。後工程にはめっきやはんだ付けなど基板が高温になる工程があり、樹脂基板では温度変化による反りや膨張が問題となっていた。マルチガラスコア基板はセ氏250度の熱でも反り量がほとんど変化せず、熱膨張率は1度当たり3ppm(0.0003%)とSi並みの水準を維持する。マルチガラスコア基板のこうした特性は、樹脂基板と比べて、Si製チップを接続する際に有利な上、大型化もしやすい。
スパコン由来の技術を活用
FICTは、新開発のマルチガラスコア基板で光電融合分野も狙う。光電融合は電気信号回路と光信号回路を融合させる技術で、期待が高まっている。今回、マルチガラスコア基板上にスーパーコンピューター(スパコン)「富岳」のプロセッサーとSi製光チップを実装し、プロセッサーと光チップの間で112Gbps(ギガビット毎秒)の高速伝送ができることを確認した。
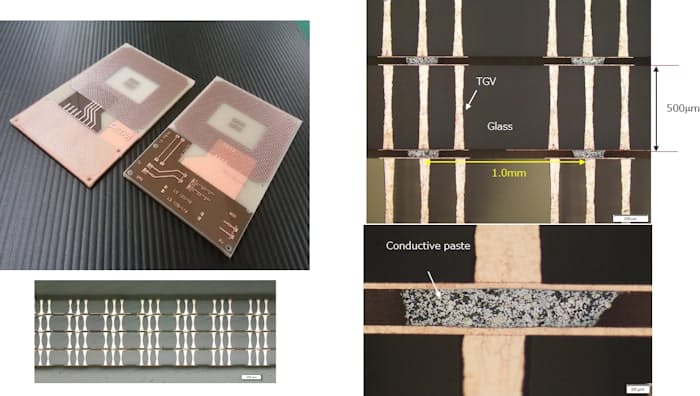
マルチコアガラス基板の基になったのは、富士通のスパコンで使われていた基板、及び基板接続技術だ。FICTの源流は1967年に発足した富士通のプリント基板事業部で、2002年に事業所を統合する形で富士通インターコネクトテクノロジーズが発足。その後、信越富士通を吸収して2022年にFICTとなった。
インテルの採用表明で脚光
ガラス基板は、既存のシリコン(Si)製インターポーザー(中間基板)を置き換えるものとして長らく期待されていたが、実際にはなかなか代替が進まなかった。この状況を一変させたのは、米Intel(インテル)だ。同社が将来の採用を表明したことで、ガラス基板はスポットライトを浴びた。
現在、チップレット集積に向けてパッケージの大型化が進むとみられており、それに伴ってインターポーザーやパッケージ基板も一層の大型化や配線の高密度化が求められることから、ガラス基板が注目されている。加えて、パッケージ基板としてガラス基板を採用すれば、パッケージ基板上にチップレットを直接並べて実装しても、Si製インターポーザーやブリッジを使った場合と同等の性能が実現できると期待されている。
ガラス基板の開発が本格化したのは2014年ごろだ。当時、Si製インターポーザーには、前工程の利用によるコスト増や、ウエハー形状による面積効率の低さといった課題があった。ガラス基板は、樹脂基板よりも高い平たん度と、Si製インターポーザーに匹敵する配線密度を実現できることから、Si製インターポーザーの代替を目指す取り組みが盛んだった。
しかし、実際には思うように普及しなかった。FICTテクノロジ本部先行技術開発部プロジェクト部長の酒井泰治氏は「Si製インターポーザーの競争力が想定以上に高かった」と語る。例えば、減価償却が終わった前工程のラインを使うことで、Si製インターポーザーの価格が下がった。また、当時のガラス基板は「要素技術や量産技術が未熟だった」(同氏)。具体的には、ガラス貫通ビアを高速で加工する方法や、薄い基板の搬送方法などが確立されていなかった。「ファブレスの半導体メーカーや垂直統合型デバイスメーカー(IDM)が採用に消極的だった」(同氏)ことも大きく影響した。
キーワード
(NIKKEI Tech Foresight/日経クロステック 松元則雄)
0 コメント:
コメントを投稿