電池コスト削減へ「ドライ電極」 全固体の遅れで脚光。 2024年2月9日 5:00
https://www.nikkei.com/prime/tech-foresight/article/DGXZQOUC0836L0Y4A200C2000000
https://www.nikkei.com/prime/tech-foresight/article/DGXZQOUC0836L0Y4A200C2000000
注目キーワード
「ドライ電極」は、リチウムイオン電池の新しい製造技術である。これまで必要だった電極の乾燥工程をなくせることが最大の特長だ。リチウムイオン電池の課題である莫大な設備投資や製造コストを削減できる切り札になり得る。電気自動車(EV)向け車載電池への適用を目指し、世界の自動車メーカーや電池メーカーが開発に注力している。
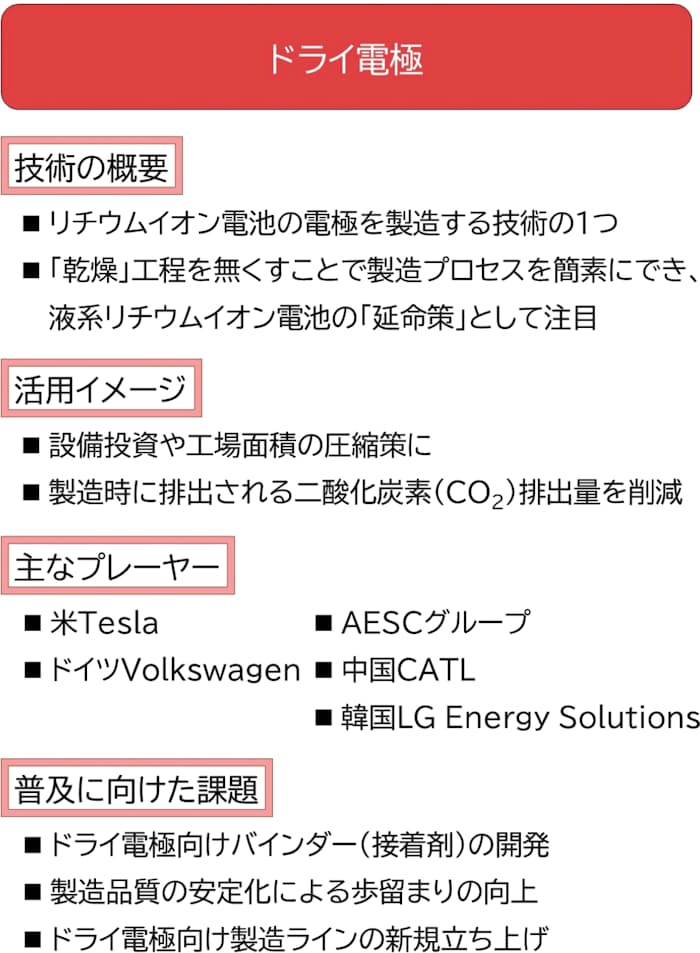
一般的なリチウムイオン電池の電極製造工程は次の通り。まず、正極材や負極材、バインダー(接着剤)などを有機溶媒に混ぜてスラリーといわれる流動性のあるペーストにする。次に、スラリーを集電体となる金属箔に塗工し、乾燥炉で熱をかけて溶媒を除去する。乾燥したものをプレスして所定の厚さに仕上げ、ロール状の電極とする。
このうち乾燥炉は長さが50〜100mに達する巨大な装置で、電池事業の投資額を莫大にし、二酸化炭素(CO₂)排出量が多くなる主因となっていた。ドイツVolkswagen(フォルクスワーゲン、VW)によると、電池製造プロセス全体で消費するエネルギーの約3割を乾燥工程が占めていたという。
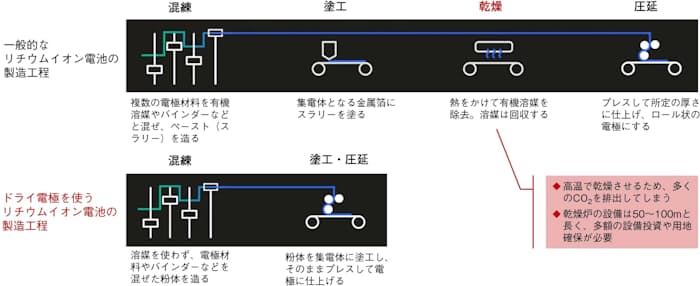
この課題と向き合ったのがドライ電極である。「ドライコーティング」や「ドライプロセス」などとも呼ばれる技術で、電極製造プロセスから乾燥工程を省いた。有機溶媒を使ったスラリーの代わりに、粉末状の電極材料を金属箔上に塗工する。
手法はいくつかある。他社に先駆けてドライ電極を実用化した米Tesla(テスラ)は、少量のバインダーの粉末を使っているようだ。電極材料とバインダーの粉末を混ぜ、熱したローラー上で集電体と電極材料を密着させ、短時間でバインダーを溶かして塗工するとの見方がある。
テスラは、米テキサス州の工場「ギガテキサス」で造る新型電池「4680」にドライ電極を適用した。実用化では先行したが、米メディアの報道によると4680電池の生産ペースが上がらず、同電池を搭載する新型EV「Cybertruck(サイバートラック)」量産のボトルネックになっているという。
VWは26年ごろに欧州・北米導入へ
持続可能で手ごろな電池を製造する上で「ゲームチェンジャー」となる技術――。ドライ電極をこう位置付けるのがVWである。同社は2024年末までに同技術の開発を完了させ、2026〜2027年に欧州と北米の電池工場に導入する計画である。乾燥炉をなくすことで、エネルギー消費の30%削減や工場床面積の15%削減などを目指す。これらにより、年間で数億ユーロの電気代を節約できると試算した。
開発は同グループの電池会社であるPowerCo(パワーコー)が担当する。印刷機メーカーのドイツKoenig&Bauer(ケーニヒアンドバウアー)と共同で、ドライ電極の製造技術を仕上げていく。粉末状の電池材料を集電体に塗工し、「髪の毛ほどの薄さの層にする」(VW)という。
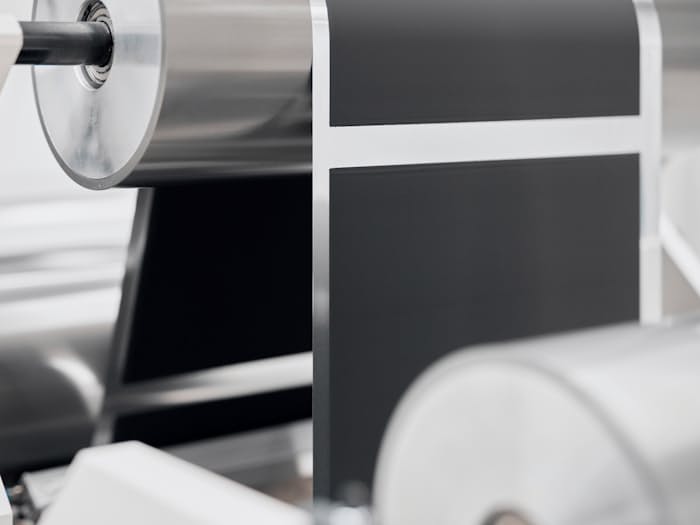
電池メーカー各社も実用化を急ぐ。全固体電池の量産計画が遅れていることが背景にある。"次世代電池の本命"は開発こそ盛んだが、量産の壁が高い。このため、当面は既存のリチウムイオン電池がEV向け電池の主流になるとの見方が強い。ドライ電極を使ってコストやCO₂排出量、工場床面積などを削減できれば、競争力に直結する。
中国・寧徳時代新能源科技(CATL)や韓国LG
Energy
Solution(LGエナジーソリューション)などをはじめとする電池メーカー各社が取り組む中で、AESCグループ(横浜市)は、茨城工場(茨城県茨城町)にドライ電極の製造ラインを構築する予定である。
茨城工場は同グループがマザー工場と位置付ける拠点。現在は「第一棟」が完成した段階で、電池の製造を2024年3月に開始する。電池製造ラインとして「第二棟」「第三棟」を計画する他、電極製造ラインも別途構築する。この電極製造ラインに「ドライ電極技術を導入し、2026年に量産を開始する」(AESCグループ幹部)という。
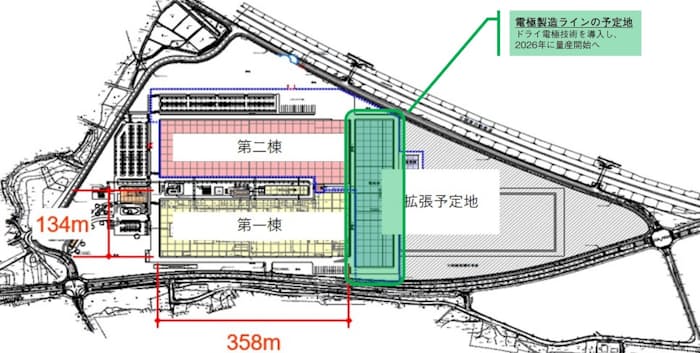
(日経クロステック/日経Automotive 久米秀尚)
0 件のコメント:
全固体ナトリウムイオン二次電池の大型と高密度のタイプを開発、現状の課題とは?材料技術
日本電気硝子は「BATTERY JAPAN 二次電池展(第16回【国際】二次電池展)」に出展し、サンプル出荷を開始した全固体ナトリウムイオン二次電池や参考出展の同電池の大型タイプと高密度タイプなどを紹介した。
日本電気硝子は「第23回 SMART ENERGY WEEK【春】」(東京ビッグサイト、2024年2月28日~3月1日)内の「BATTERY JAPAN 二次電池展(第16回【国際】二次電池展)」に出展し、サンプル出荷を開始した全固体ナトリウムイオン二次電池(以下、NIB)や参考出展のNIBの大型タイプと高密度タイプなどを紹介した。
生産プロセスの見直しで歩留まりを改善しサンプル出荷を実現
同社のNIBは、正極、負極、固体電解質の全てが「安定した酸化物」により構成され、これらが独自の結晶化ガラス技術により強固に一体化した電池だ。過酷な環境下(-40~+200℃)で作動し、発火や有毒ガス発生のリスクがない他、資源確保への懸念を要しない材料であるナトリウムを用いた全固体電池となっている。サンプル出荷を開始したNIBは出力電圧が3Vで容量が200mAhの標準タイプだ。
サンプル出荷を開始したNIBの標準タイプ[クリックで拡大] 出所:日本電気硝子
日本電気硝子の説明員は「2023年の二次電池展でNIB標準タイプの開発品を出展した際には、製造プロセスを最適化できておらず、生産品の性能にバラツキがあった。2023~2024年にかけて、製造プロセスを見直すことにより、充放電を1000サイクル以上可能な一定の性能を持つNIB標準タイプを小ロット生産できるようになり、サンプル出荷に踏み切った。小ロットでも導入実績をつくり、認知度を上げていきたい」と話す。
会場ではエスペックの小型環境試験機「SU-242」を用いてNIB標準タイプが-40℃と+150℃で動作することを披露した。同社のNIBは、ガラスの軟化流動性を利用して正極や負極、固体電解質を強固に一体化することで、高いイオン伝導性を実現しているため、低温/高温の環境を問わず安定した動作が行える。
エスペックの小型環境試験機「SU-242」を用いてNIB標準タイプが-40℃(左)と+150℃(右)で動作することを披露[クリックで拡大]
さらに、クギを刺したNIB標準タイプも展示し、電池材料が全て無機酸化物で構成されているため、使用時と製造時に発火や有毒物質発生の可能性がないことも紹介した。
クギを刺したNIB標準タイプも展示[クリックで拡大]
参考出展したNIBの大型タイプはA4サイズで、高密度タイプは容量が500mAhとなっている。「現状、NIBの大型タイプと高密度タイプはいずれも生産プロセスが最適化されておらず、一定の性能を有すものを安定的に生産できない。今回は、容量が数十Ahとなる大型タイプや500mAhの高密度タイプを見せることで、当社のNIBの可能性を披露している。今後、両タイプの製造プロセスの見直しなどを進めていく。大型タイプに関しては、電気自動車(EV)市場で展開できる可能性があるため期待している」と語った。
なお、素材メーカーである同社は、二次電池メーカーなどと協業して、NIBの量産を行うことも視野に入れているという。
全固体NIBの大型タイプ[クリックで拡大]
全固体NIBの標準タイプ(左)と高密度タイプ(右)[クリックで拡大]
⇒その他の「材料技術」の記事はこちら
関連記事
関連リンク
Copyright © ITmedia, Inc. All Rights Reserved.
Special
- PR -手戻り減! 設計業務のリモート化がもたらした魅力的な改善効果
ランダム読み出し速度20倍! 車載MCU/SoCの外付けに最適なNORフラッシュ
エネルギー効率を最大化する太陽光発電システムと大容量蓄電池の使い方とは
医療機器開発を取り巻く課題は山積 複雑化する規制に対する最適な環境とは
地球シミュレータの次は「四次元仮想地球」 JAMSTEC新計画に見るHPCの進化
プロダクト×OT×ITのつながりが革新の原動力、製造と物流の課題を解決する
人手不足の中で“紙”の点検作業は維持できるのか その現実的な対策
GaNも強化中! オンボードチャージャーの電力密度向上に挑むインフィニオン
SiCパワーデバイスやエッジAIをけん引するST サステナビリティー経営も追求
絶縁バイアス電源を9割小型化! 高い電力密度を実現する最新の電力変換IC